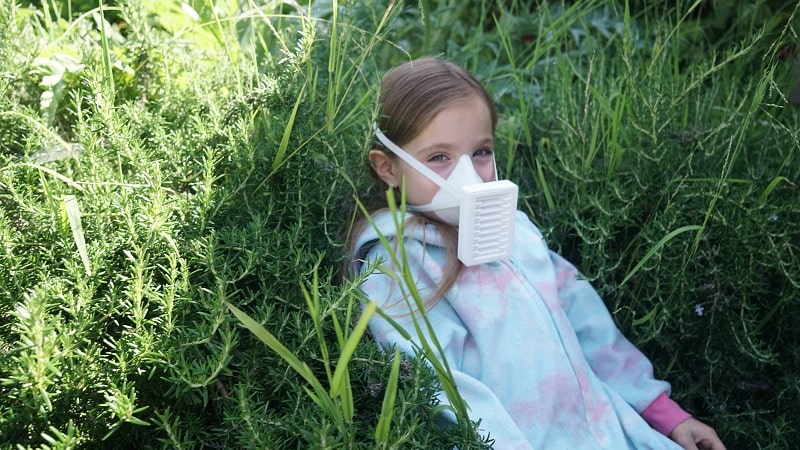
Does it really take a team of rocket scientists to rapidly engineer a top-notch line of personal protective equipment (PPE) to protect against COVID-19 spread? And then to open source its production designs for the benefit of anyone with access to a 3D printer?
The answer: not necessarily, but it sure can help.
That’s the latest good news on the pandemic front from the technology and innovation team at the National Aeronautics and Space Administration’s (NASA) Jet Propulsion Laboratory (JPL).
The team led by Tom Soderstrom, IT Chief Innovation Officer at JPL, set out in late March to quickly iterate open source designs and production techniques for the types of high-quality respirator masks that often have been in very short supply during the coronavirus pandemic.
More than 30 rapid development cycles and roughly five weeks later, the results speak for themselves.
The bottom line – if you’re just the tiniest bit crafty, and have access to a 3D printer, you can make one of three models of washable, reusable, comfortable respirator masks suitable for general and professional applications. And because they can be home-made, they don’t disrupt the normal medical supply chain for PPE. Total cost per mask? About two bucks.
The product designs and plans are free for anyone to use. You can find them at: https://github.com/nasa-jpl/COVID-19-respirators, where the designs, 3D print files, detailed test results, build and test instructions, and the development team are listed. The respirator masks are designed to meet or exceed N-95 standards, but have not yet been certified by the National Institute for Occupational Safety and Health (NIOSH).
Speedy Keys to the Project
Soderstrom, a 14-year JPL veteran, told MeriTalk earlier this month that the respirator project began with a query from JPL Chief Information Officer Randi Levin – could such a thing be done? Because it’s Soderstrom’s job to investigate what he calls “technology waves” and understand how they can be harnessed for JPL’s benefit, Soderstrom and a team of six colleagues naturally dived into the project.
From the beginning, they were driven by the start-up ethos that rapid iteration and rapid testing of concepts and prototypes paves the fastest path to success.
True to the grass-roots nature of the effort, it began as a voluntary project, and was executed with inexpensive (about $750 each) JPL 3D printers that three team members brought to their homes to use. Some of the questions answered along the way: Can you use highly available nontraditional materials so not to disrupt the medical supply chain? Yes, by being creative and flexible. Can you 3D print respirator filters? No, but you can cut out 18 of them from a vacuum bag. Or you can use commercial filters, if you have them. What gives a mask a more comfortable fit? Try flexible 3D printing materials or simply a piece of weather stripping from the home improvement store.
The final set of respirator products were finished in well under 1,000 combined work hours from team members, and a viable path to making inexpensive life-saving PPE is being shared with the world – for free. The team – that also includes Kalind Carpenter, Eric Contreras, Doug Hofmann, Chris Mattmann, Yazmin Melo, and Don Ruffatto – has since farmed out samples of the products to doctors and other professionals, and is seeking NIOSH certification for the respirators.
Because the masks can be made anywhere around the world, distribution bottlenecks for this category of PPE can be lessened amid the pandemic-driven demand. And the open source availability of the designs means they can be further improved upon by anyone who wants to take the idea further – hobbyists, tinkerers, scientists, engineers – maybe even you. You could also join the JPL team in imagining what you could do by adding sensors that can measure – well, just about anything – to the respirator masks.
You don’t have to be a rocket scientist…but it never hurts.